In the following overview I give the interested reader a summary of the technologies and innovations I use.
Preamble
If you compare guitars to cars, it’s interesting how much cars have evolved since the 1950s compared to guitars. What both have in common is people’s enthusiasm for the old models. With guitars this is then called „vintage“, with cars „oldtimer“ and in both areas there are collectors who let their passion cost them a lot of money.
The possibilities of further development of the guitar are much more limited than with the car. This has the great advantage that guitars can be easily repaired and restored even after many years. Nevertheless, guitars have changed a lot over the decades: pickups, tremolos, fret wires, neck geometries, strings, tuners… In terms of playability and sound variations, one has an infinite choice of possibilities today.
And here is my intention: Breaking new ground to enhance the sound, ergonomics, look and feel of the guitar. I’m constantly working on solutions that replace or further develop existing technologies. That’s simply what I learned in my 30 years in automotive development: Doing things differently, not just so they are different, but so they feel and work better!
Wood selection
I prefer to make the body and the neck from one piece of wood. Regional woods that have been air-dried for many years are used.
Titanium truss rod
To reduce weight, I make truss rods from 5mm diameter titanium. In order to cut out as little wood as possible in the middle of the neck, I insert the truss rods into the neck from below. Optionally I offer my guitars with an open truss rod slot.
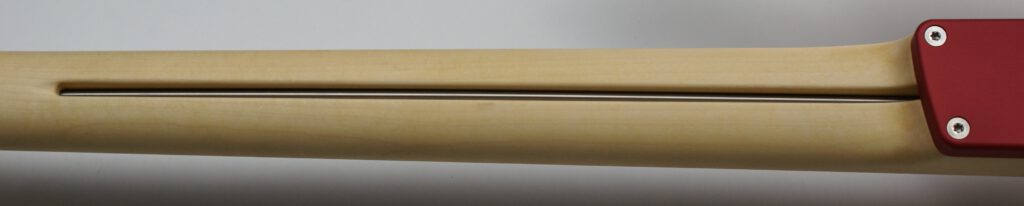
The truss rods of the ORION and the SIRIUS are bolted to the aluminium center section. This continuous metal structure supports a long sustain.
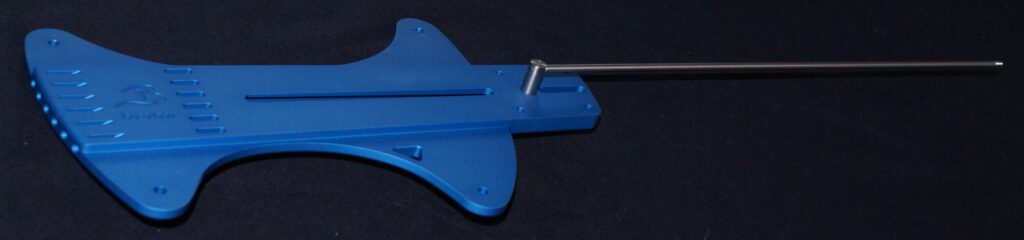
Fretboard and truss rod cover
The fretboard and truss rod cover integrated into the neck are made from one continuous piece of wood. The wood grain in the fingerboard continues seamlessly in the cover. A very elaborate and valuable option that is standard in the ORION.
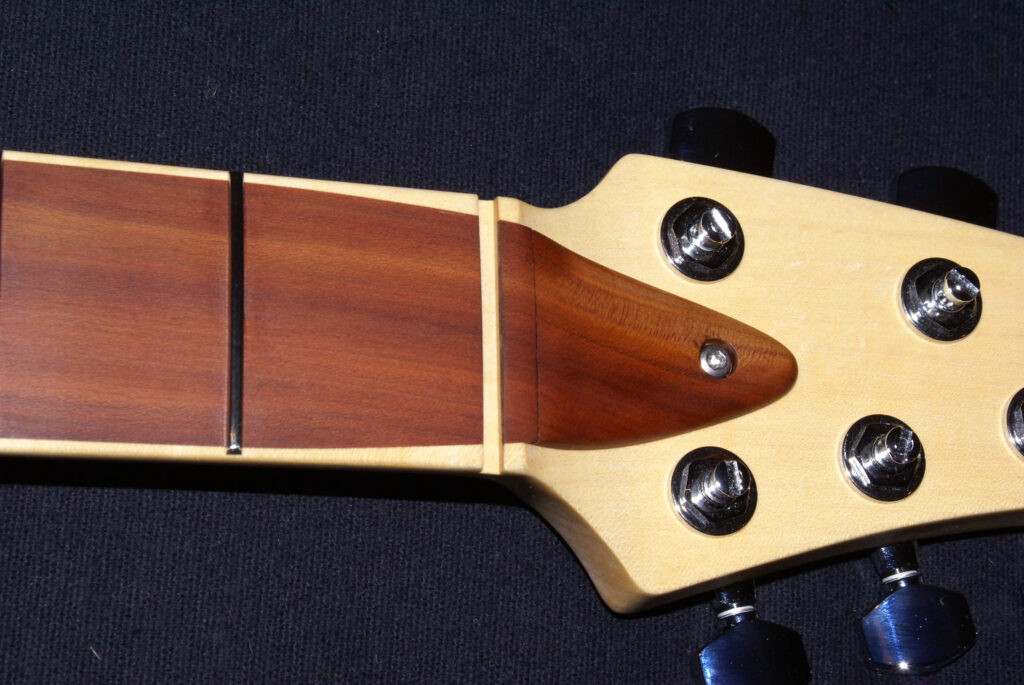

Fretting
As a standard, I use stainless steel fretwire. This is much less abrasive and does not oxidize – in contrary to nickel silver.
The slots for the frets are not milled to the edge, so that the bar of the fret wire, which is pressed into the wood, is not visible and therefore not feelable.
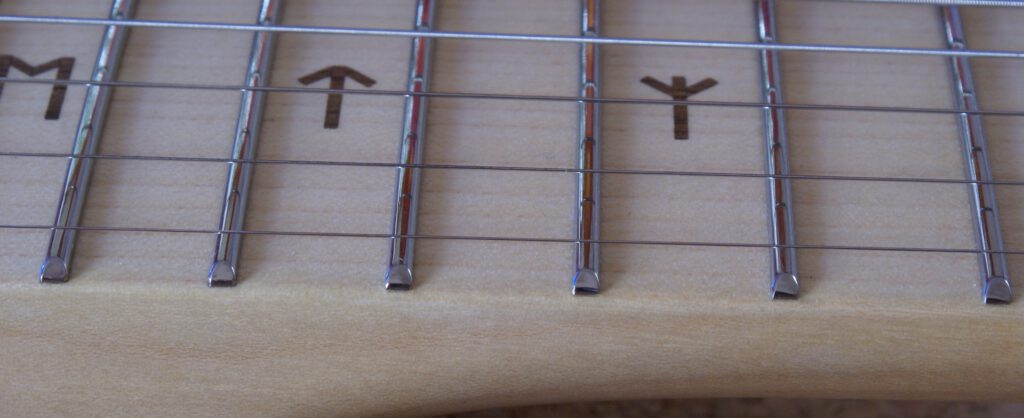
Moveable Pickups
The pickups of the ORION and the SIRIUS are smoothly movable on an aluminium rail. This covers a huge sound spectrum. The rail is adjustable in height and angle of the pickups. If the guitars are configured with 2 single-coil pickups, they form a humbucker when moved together. For this purpose, the pickups can be connected in series or in parallel, which again allows additional sound variations.


Electrics
I prefer to use pickups from Harry Häussel. Own pickups with a special design are in development.
For the electrics only proven quality components are used. In the ORION and the SIRIUS I use especially small and valuable components from Bourns (pots) and Grayhill (switches).
The electrical compartment and the cavities for the pickups are completely shielded with high-quality conductive lacquer. This keeps the noise at a low level even with single-coil pickups.
My Lockdown-Board: With this I can emulate any standard electrical system. The outputs of the pickups go directly into the board. Here I can tune which circuit, which poti values and which capacitors fit the guitar optimally. Only after this tuning, the selected electrics are soldered into the guitar.
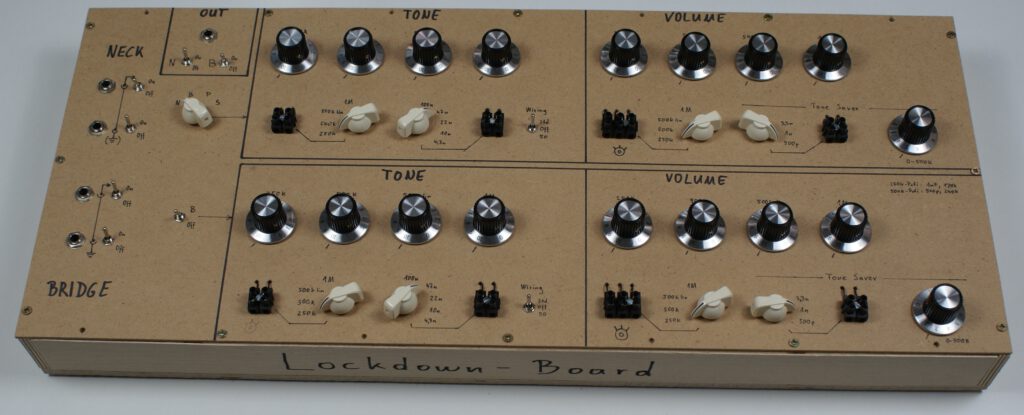
Inlays
One of my passions is the design and implementation of inlay work. I like to take ideas and suggestions from my customers. For the inlays materials of all kinds can be used: Wood, bone, horn, mother of pearl, coral, metal, amber, glass, stone. There are no limits to the imagination.
Aesthetics
The small fine details make the difference and sometimes cost a lot of effort in manual labor.
I usually make pickup caps out of wood and avoid using frames for mounting.
The potentiometer knobs are recessed in the body. Screws and nuts are attached with great effort largely invisible.
Optionally, I offer a value package in which numerous components such as screw heads are polished extra or otherwise refined on the surface.
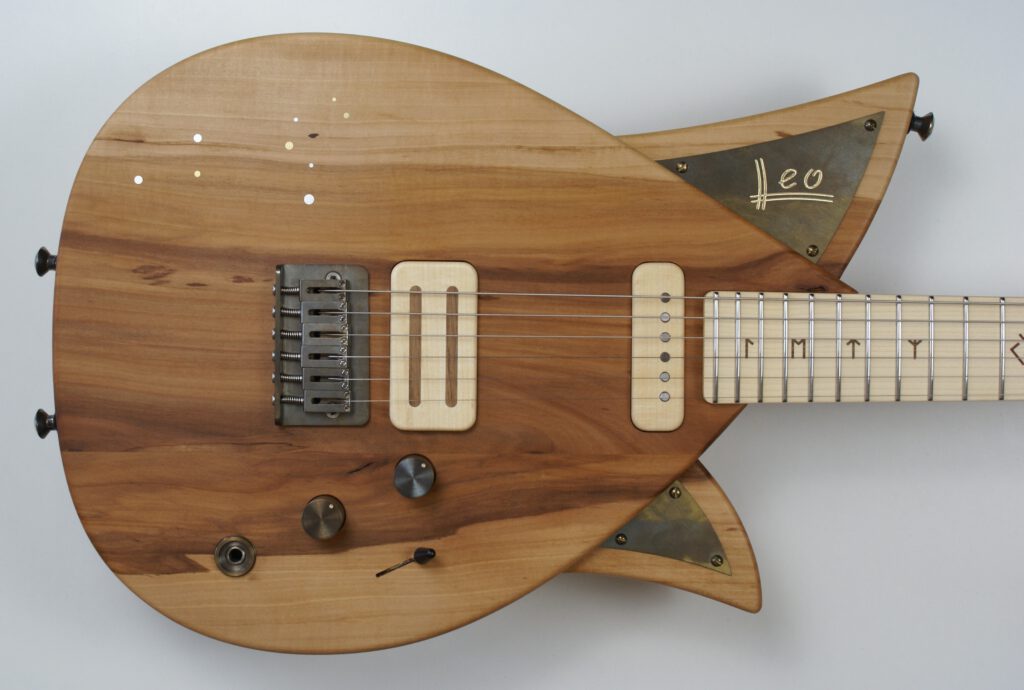
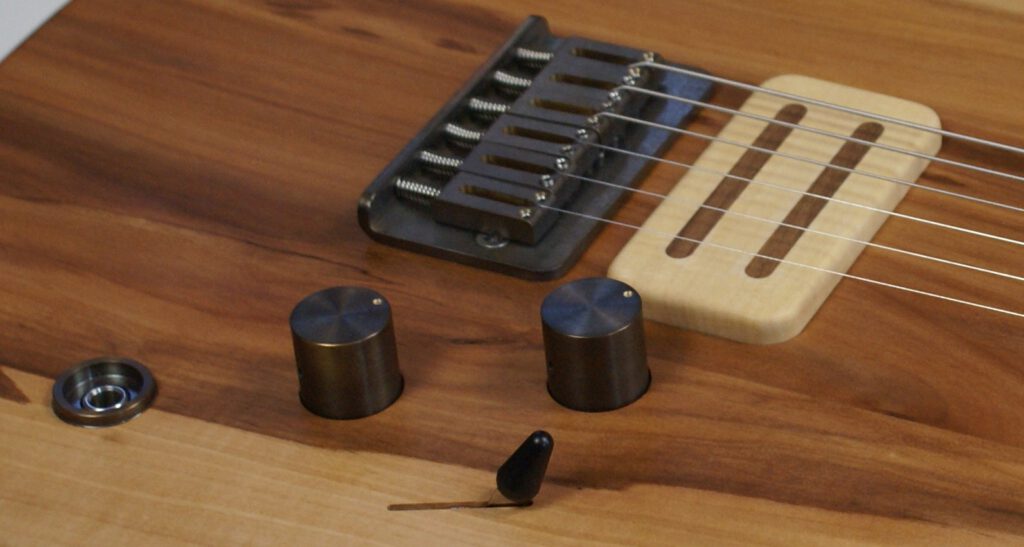
Ergonomics and feel
Superior ergonomics and feel of my instruments is very important to me. It simply has to be fun to pick up the guitar and not let go for hours.
The decisive factor here is the feel to the touch. All wood surfaces are sanded and oiled in numerous passes. The oiled surface can then be polished to the desired surface feel. In extreme cases, the smoothness of a painted surface can also be achieved.
Ergonomics: The guitar must be well balanced on the strap and when sitting. I prefer to position the volume pot directly under the bridge pickup. This is optimal for guitarists who work with the pot while playing.
Setup and compound radius: The decisive tenths of a millimeter
The ideal setup of a guitar is a philosophy in itself. Here, every luthier has his own techniques and preferences. I prefer to do the final setup of a guitar in spring or fall. Here you are between the extremes of humidity.
Neck radius: Here I strictly follow the mathematics and always use a compound radius.
Copyright © 2008-2025 Peter Bachmaier